5 Strategies to Scale Production Capacity without Compromising Quality
Every businessman wants to grow their business. Likewise, every manufacturing business wishes to expand their output to earn more and meet high demand in the market. Obviously, it is important for them to scale production capacity inorder to grow bigger and meet increased demand in the market.
At the same time, if the manufacturer makes more products by compromising quality just to meet high market demand, in the desire to make a profit out of it, they will definitely lose their goodwill in the market. They won’t survive thereafter. It is essential to scale your production without compromising quality to be successful in the market for the long run.
It has been found that 75% of buyers don’t purchase a product again if they experience low quality, according to a survey conducted by Nielsen. In 2015, Volkswagen installed software in its diesel engines that could cheat emission tests, which are mandatory to meet environmental regulations. Eventually, this act was discovered, impacting Volkswagen’s reputation in front of their customers and resulting in billions of dollars in fines.
What is Production Capacity?
Production capacity is about a manufacturing company’s ability to produce a maximum number of products using its resources. How to calculate your production? The capacity of a manufacturing business varies significantly depending on the number of machines available, workforce, material availability, and workflow.
For example, let’s consider a mobile manufacturing company. Their capacity means the maximum number of smartphones they can produce within a given timeframe, let’s say one month.
If the company’s output is eight thousand, it means they can produce up to eight thousand units in a month using their resources, including machines, workforce, and materials. The one-month timeframe may cover production line downtime occurring due to machine failure, scarcity of material, workforce, and maintenance schedules.
It is important to assess the output capacity of every company, whether it is a manufacturing or service providing company. Because the assessment effectively helps in planning, allocating materials, streamlining workflow, and meeting customer demand. Capacity planning must take place in every business.
Assessing Current Production Processes
It is important to have a clear understanding of current production processes before thinking about increasing output. Let’s start with material acquisition. How much material are you acquiring in a month or year? Assess the efficiency of machines, labor, and downtime, such as maintenance schedules, and repairs.
Using all the above metrics, you can calculate the current capacity. It provides the maximum number of products you can produce with your existing resources. It gives a clear picture of current capabilities.
After understanding your current capacity, you can start the analysis of your processes. Identify bottlenecks, inefficiencies leading to rework, and wastages. Now is the time to fix all these pain points. Come up with proper solutions to alleviate these issues and take steps toward optimization.
Machine breakdowns, unplanned downtimes, quality issues, inefficient processes, defective raw materials, human error, and inefficient quality control measures result in production losses. The maximum output that a machine or a production line can achieve in a timeframe is called machine capacity. Calculating this is essential to measure overall capacity.
5 Effective Strategies to Increase Production Capacity
Every businessman has to increase their production over time based on increased demand for the products in the market. Also, it is important for them to stay on track and lead in the market competition.
Obviously, without increasing output, they cannot boost profitability. But as we discussed, increasing capacity by compromising quality is also not an option. So as a manufacturer, what can you do?
Let’s dive into five effective strategies to increase your production without altering product quality. These strategies will help you understand many aspects of your production line, where you can make improvements, what to eliminate and many more.
Let’s get started.
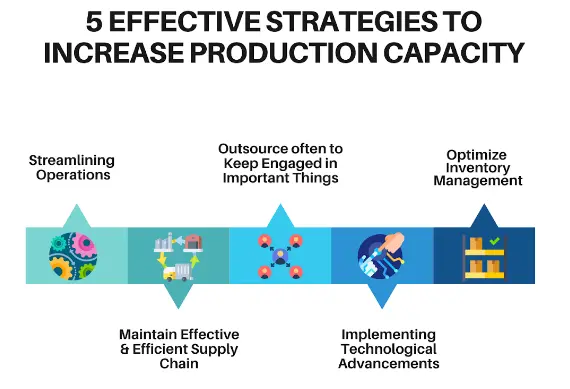
1. Streamline Operations
Optimizing the workflow across your production line can significantly enhance efficiency. This includes managing material acquisition, sequencing workstations, allocating workforce, and scheduling time. Streamlining these aspects minimizes downtime and improves productivity.
Utilizing AI and advanced technologies can automate repetitive tasks, optimize resource allocation, and facilitate real-time collaboration. For example, if you run a manufacturing unit for electronic gadgets, arranging workstations to minimize waste and eliminate inefficiencies can cut order-to-delivery time by 30% and boost production capacity by 20%.
Integrating lean manufacturing principles, such as the 5S methodology (Sort, Set in order, Shine, Standardize, Sustain), can further streamline operations. Continuously analyze and improve processes, to identify bottlenecks and eliminate non-value-added activities. This proactive approach ensures a smooth workflow and reduces delays, directly impacting production capacity.
2. Maintain Effective & Efficient Supply Chain
An efficient supply chain is crucial for increasing production capacity, especially during peak demand periods. Implementing methods like the Just-in-Time (JIT) inventory model allows quick adaptation to changing demands. Reliable suppliers and improved coordination among stakeholders can yield substantial benefits.
For instance, by maintaining a robust supply chain, a company can react swiftly to market changes, ensuring production processes remain uninterrupted and quality standards are upheld.
Building strong relationships with suppliers through regular communication and performance reviews can foster a more resilient supply chain. Additionally, incorporating advanced supply chain management software can enhance visibility, allowing for better demand forecasting and inventory planning. These tools can predict potential disruptions and provide contingency plans, ensuring smooth operations even during unforeseen events.
3. Outsource often to Keep Engaged in Important Things
Outsourcing non-core activities to specialized external companies can free up resources and enhance production capacity. This approach reduces capital investment in additional facilities and allows businesses to leverage advanced technologies and expertise from other firms.
Consider a pharmaceutical company that outsources its packaging operations. By doing so, it can focus more on research and development while reducing overall time and costs associated with packaging. This strategy not only speeds up the production process but also ensures better allocation of resources to core activities. Discover the elegance of our collection featuring the best Hublot replica watches. Each fake hublot watch combines luxury and affordability, allowing you to set the trend effortlessly.
When outsourcing, it’s crucial to select reliable partners with a proven track record. Establishing clear communication channels and setting performance metrics can help maintain quality and efficiency. Outsourcing can also provide access to innovative solutions and industry best practices, further enhancing the overall production process.
4. Implementing Technological Advancements
Integrating new technologies into your production process can significantly boost capacity. Advanced machinery and automated systems can streamline operations, improve efficiency, and maximize output.
For example, a food processing company that installs an automated packaging system can reduce the workforce needed in that unit. The result is a 50% increase in packaging speed, an 80% reduction in errors, and a substantial boost in overall production capacity.
Investing in Industry 4.0 technologies, such as the Internet of Things (IoT), big data analytics, and robotics, can revolutionize manufacturing processes. IoT devices can provide real-time data on equipment performance and product quality, allowing for predictive maintenance and reducing downtime. Big data analytics can optimize production schedules and resource allocation, while robotics can handle repetitive tasks with high precision and speed, further increasing production capacity.
5. Optimize Inventory Management
Effective inventory management is vital for increasing production capacity. Implementing real-time tracking systems helps monitor inventory levels throughout the supply chain, enabling you to adjust production based on demand accurately.
Using historical data for demand forecasting, maintaining strong supplier relationships, reducing waste, implementing quality control at each stage, and investing in scalable inventory management infrastructure are all critical components of optimizing inventory management. Providing employee training to handle these systems effectively also ensures smoother operations.
Adopting inventory management software that integrates with your ERP system can provide a unified view of your entire supply chain. This visibility allows for better coordination between production, procurement, and sales teams. Techniques such as ABC analysis, which categorizes inventory based on value and turnover rate, can help prioritize management efforts on the most critical items, ensuring optimal inventory levels and reducing carrying costs.
How to Ensure Product Quality and Customer Satisfaction after Increasing Production Capacity?
While increasing production capacity is crucial for business growth, maintaining product quality and customer satisfaction is equally important. As we’ve seen, compromising quality can lead to significant losses in customer trust and market share.
Here are some effective strategies to ensure product quality and customer satisfaction as you scale up your production:
Implement robust quality control measures:
Establish stringent quality checks at every stage of production. This includes incoming material inspection, in-process checks, and final product testing. Utilize statistical process control (SPC) techniques to monitor production processes and identify potential quality issues before they escalate.
Invest in employee training:
As you scale up, ensure your workforce is well-trained in quality management practices. Regular training sessions on quality standards, operating procedures, and the use of quality control tools can significantly reduce human errors and maintain consistency in product quality.
Leverage technology for quality assurance:
Implement advanced quality management systems (QMS) that integrate with your production processes. These systems can automate quality checks, provide real-time data on product quality, and help in quick identification and resolution of issues.
Maintain open communication channels with customers:
Regularly seek customer feedback through surveys, focus groups, or direct interactions. This helps in identifying areas of improvement and addressing customer concerns proactively.
Implement a robust traceability system:
In case of quality issues, a good traceability system can help quickly identify the source of the problem, minimize its impact, and implement corrective actions efficiently.
Continuous improvement:
Adopt methodologies like Six Sigma or Total Quality Management (TQM) to foster a culture of continuous improvement. These approaches help in identifying and eliminating the root causes of quality issues, leading to sustained quality improvements over time.
With the implementation of these strategies, manufacturers can ensure that the increase in production capacity does not come at the cost of product quality or customer satisfaction. In today’s competitive market, maintaining high-quality standards is not just about meeting customer expectations – it’s about exceeding them consistently.
Conclusion
Increasing production capacity can be achieved without compromising the quality of products. Production increase requires proper planning, streamlined workflow, effective coordination and communication among stakeholders and adopting technologies for improved performance.
Follow production strategies that boost your profitability through increasing production capacity but without sacrificing product quality. Quality of the product can only gain more reputation and consumer satisfaction. As a result, your brand will stay in the market on the top level ever.
Leave a Comment